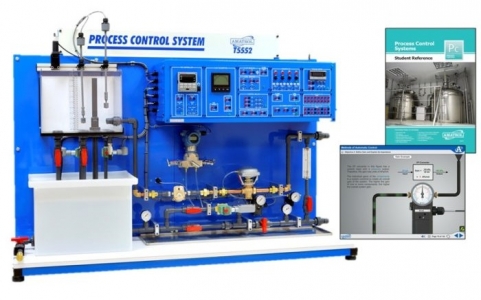
Level / Flow Process Control Learning System
Model: T5552
Manufacturer: Amatrol
Introducion:
- Process control systems provide precise control of liquids and gases in industrial areas including power generation, petrochemicals, food processing, and manufacturing. These systems control liquid and gas variables like flow rate, pressure, temperature, liquid level, density, and pH levels. Amatrol’s Level and Flow Process Control training system covers two types of process control systems, flow and liquid level.
Training Program:
- Process Control Concepts
- Safety
- Manual Control
- Instrument Tags
- Piping and Instrumentation Diagrams
- Loop Controllers
- Final Control Elements
- Level Measurement
- Liquid Level Control
- Methods of Automatic Control
- Basic Flow Measurement and Control
- Control Loop Performance
Technical Specification:
- Workstation: 66” L x 46” H x 28” W
- Centrifugal Pump
- Electric Motor, single phase
- Proportional Control Valve, pneumatically-operated
- I/P Converter, 4-20ma input
- Pneumatic Regulator and Pressure Gauge
- Reservoir Tank, 10 gal.
- Process Tank, 5 gal.
- Piping Network
- Process Meter
- PLC I/O Interface
- Relay Control Unit
- Interactive Multimedia Curriculum
Option:
- Process Control Connection Kit (Required to connect any of the following systems: T5552, T5553, T5554, T5555. One kit required to connect 2 systems, 3 kits required to connect all 4 systems.)
- Smart Flow Transmitter Learning System
- Ultrasonic Liquid Level Learning System
- PID Controller Module
- Foundation Fieldbus Process Control 1 Learning System - AB L16
- HART Process Control 1 Learning System
- Process Visualization Control 1 Learning System
Buy product
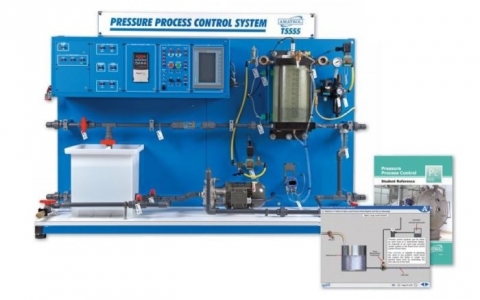
Pressure Process Control Learning System
Model: T5555
Manufacturer: Amatrol
Introducion:
- (VFD) that are found in real-world industrial fields such as pharmaceutical, bio-technology, and power generation!
Training Program:
- Process Control Concepts
- Instrument Tags
- Block Diagrams
- Piping and Instrumentation Diagrams
- Instrument Index
- Final Control Elements
- Pressure Measurement
- Loop Control Devices
- HMI Panel Operation
- Pressure Control Systems
- Process System Alarms
- Automatic Control Methods
- Performance Concepts
- Control Loop Performance
- Open- & Closed-Loop Tuning
Technical Specification:
- Tank Assembly
- Gas Exhaust Assembly
- Reservoir Tank Assembly
- Motor Assembly
- VFD-PLC Interface Assembly
- Touchscreen Panel Assembly
- VFD Panel Assembly
- Control Console
- Electric Proportional Valve
- Piezoelectric Pressure Sensor
- Lockout/Tagout and Padlock
- Power Cord
- Multimedia Curriculum
- Utilities Required:
- 110/230 VAC, 60/50 Hz, Power Outlet
- Water Source
- Compressed Air Supply
Option:
- Process Control Connection Kit (Required to connect any of the following systems: T5552, T5553, T5554, T5555. One kit required to connect 2 systems, 3 kits required to connect all 4 systems.)
- Multimedia Curriculum (Pressure Process Control Learning)
Buy product
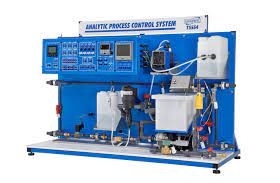
Analytical Process Control Learning System
Model: T5554
Manufacturer: Amatrol
Introducion:
- The Analytical Process Control training system includes a tabletop workstation with a control panel, PLC interface, and industrial pumps, tanks, and piping. The system allows learners to explore a wide range of topics, including analytical process control, pH electrodes, pH meters and transmitters, loop controllers, and more!
Training Program:
- Process Control Concepts
- Instrument Tags
- Piping and Instrument Diagrams
- Analytical Process Control
- pH Electrodes
- pH Meters and Transmittiers
- Loop Controllers
- pH Control Systems
- Methods of Automatic Control
- Control Loop Performance
Technical Specification:
- Table-top Workstation
- Control Panel
- PLC Interface Panel
- Metering Pump
- Injector Pump
- Continuous Stirred Tank Reactor (CSTR)
- pH Transmittier
- pH Probe
- Reagent Tanks (2)
- Piping By-Pass Network
- Additional Requirements:
- PID Controller Module – Single Loop or PID Controller Module – Dual Loop
- 6’ Workstation
Option;
- Process Control Connection Kit (Required to connect any of the following systems: T5552, T5553, T5554, T5555. One kit required to connect 2 systems, 3 kits required to connect all 4 systems.)
Buy product

Temperature Process Control Learning System
Model: T5553
Manufacturer: Amatrol
Introducion:
- Amatrol’s Temperature Process Control Learning System teaches learners how to install, calibrate, operate, adjust, and tune thermal process control systems in a wide variety of industrial applications, including food processing, chemical manufacturing, and bio-technology. Process control systems provide precise control of liquids and gases.
Training Program:
- Process Control Concepts
- Instrument Tags
- Piping and Instrumentation Diagrams
- Thermal Energy
- Heat Exchangers
- Chillers
- Loop Controllers
- Current-to-Air Pressure (I/P) Converters
- Proportional Control Valves
- Thermocouples
- Resistive Temperature Detectors (RTDs)
- Thermistors
- Temperature Transmitters
- Temperature Control
- Methods of Automatic Control
- Control Loop Performance
Technical Specification:
- Process Control Workstation
- Control Unit
- Process Indicator / Transmittier
- PLC I/O Interface
- Power Supply
- Operator Interface Station
- Heating Loop Network
- Centrifugal Pump
- Electric Motor, Single-Phase
- 3-Way Proportional Control Valve
- Pneumatic Regulator
- Reservoir Tank, 3 gal
- Piping System
- Throttle Valve
- Process Instrumentation RTD, 100 ohm pt.
- Temperature Gauges (6)
- Rotameter Flow Indicators
- Chiller
- Additional Requirements:
- PID Controller Module – Single Loop or PID Controller Module – Dual Loop
- 6’ Workstation
Option:
- Process Control Connection Kit (Required to connect any of the following systems: T5552, T5553, T5554, T5555. One kit required to connect 2 systems, 3 kits required to connect all 4 systems.)
- Temperature Process Control eBook
- Three-Channel Data Acquisition Learning System
- Two-Channel Temperature Transmitter Module
Buy product
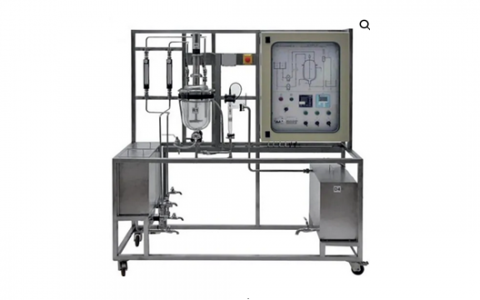
Level control system by means of PLC & touchscreen
Model:
Manufacturer: Langlois
Introducion:
- REGULEAU is a level control system relying on a PLC and touchscreen, which can be used in three detection modes, using: 3 binary floats; 4 height-adjustable conductive probes; 1 4-20mA hydrostatic pressure sensor
Training Program:
- Studying, putting into service, getting started and setting of the system
- Understanding the setting and the programming by PLC
- Understanding the PID level regulation, probes and sensors
Technical Specification:
- 1 100L lower tank
- 1 transparent 60L upper tank, graduated in cm
- 3 level sensors with binary float (24V-3A).
- 4 immersed conductive probes.
- 1 hydrostatic pressure sensor.
- Cabinet and console
- 1 5.7” TFT touchscreen
- 1 4-port RJ45 Ethernet hub
- 1 three-phase speed controller
- 1 PLC with software, fitted with a TCP/IP interface for the RJ45 link to a PC and the touchscreen.
- 1 Vijeo Designer® software with a complete monitoring program
- 1 30mA residual current circuit breaker. thermal-magnetic circuit breakers
- 230V power supply
Buy product
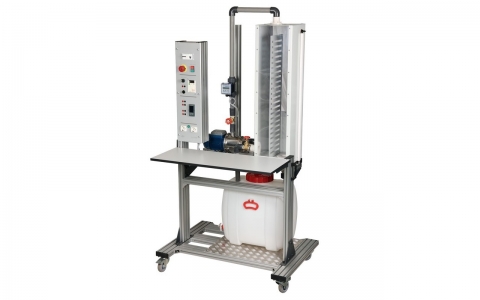
Regulation of level and flow rate by PID
Model: MAQ-ND
Manufacturer: Langlois
Introducion:
- It groups two types of regulation:
- Regulation by PID of water level with 4-20mA hydrostatic pressure sensor.
- Regulation by PID of water flow rate with 4-20mA analogue flowmeter.
Training Program:
- Putting an electrical installation into service.
- Learning about and using a PID regulator, a hydrostatic sensor, and a 4-20mA flowmeter.
- Using a regulation system for water level and flow rate by analogue signal 4-20mA.
- Using and configuring a speed variator locally and from programming software.
- Measuring, analysing and interpreting analogue signals.
- Learning industrial maintenance.
Technical Specification:
- Frame made of matt anodized aluminium mounted on four casters, two with brakes.
- A bottom tank of 100L.
- One top tank of 60L with 2 transparent sides.
- One three-phase motor pump 230V/400V with a power of 750W.
- One rotary valve for manually adjusting the water flow rate at the pump outlet.
- One rotary valve for adjusting the water leak level at the tank outlet.
- One ¼ turn valve for rapid draining of the tank.
- One 4-20mA flowmeter with integrated digital display.
- One hydrostatic pressure sensor 4-20mA directly mounted on the tank wall.
- One electrical console
- Melamine shelf with dimensions 1000 x 400 mm.
Option:
- PID communicating with software for drawing curves
- COMPUTER HOLDER OPTIONS
- FLOW INDICATOR WITH FLOAT
Buy product
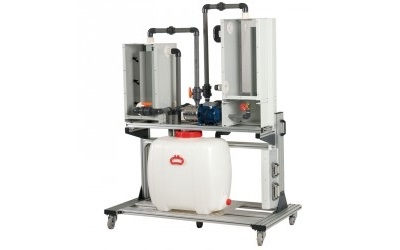
Pumping systems with supervision and regulation
Model: HYDRO-1-C
Manufacturer: Langlois
Introducion:
- These 4 versions of pumping systems are supplied wired and configured. Accordingto the model selected, the student can study supervision, level regulation and flow rate regulation. System supplied fully functional with examples of programming. A CD contains the user instructions, tutorials and the controller, HMI and speed drive programs.
Training Program:
- Study of the supervision of an industrial pumping station
- Study of the regulation of water level by all-or-nothing float sensor
- Study of the regulation of water level by hydrostatic sensor 4-20mA
- Study of the regulation of water flow rate by flowmeter 4-20mA
- To understand the operation of an industrial pumping system
- To take industrial measurements of electrical values
- To produce a PID program with a controller PLC
- To produce a PID program with a 4-20mA regulatotr
- To study Ethernet / IP addressing
- To learn how to use and configure a speed variator
- To perform industrial maintenance operations
- To study the analogue signal 4-20mA
Technical Specification:
- Aluminium frame with casters
- 1 bottom tank of 150L
- 2 top tanks (transparent sides) each with: 3 float level sensors, 1 multiple turn draining valve.
- 1 overflow safety system.
- 2 three-phase motor pumps 230/400V (1hp). Safety device for no load pumping and reversal of rotation direction. Equipped with 2 multiple turn valves.
- 1 electrical cabinet with residual current and thermal-magnetic protective devices
- 1 Schneider® controller M221(PLC) with integrated PID and analogue board
- 1 Ethernet colour touch screen 5.7".
- 1 Vijeo Designer® supervision program
- 1 three-phase speed variator with its programming software Somove® (configured for level regulation)
- 1 three-phase speed variator with its programming software Somove® (configured for flow rate regulation)
- 1 water level sensor 4-20mA – Configured for water height of 600mm
- 1 flowmeter 4-20mA – Display and programming buttons on front
- 1 PID regulator with screen and programming buttons on front.
Option:
- INDICATEUR DE DEBIT A FLOTTEUR
- ALL OR NOTHING FLOW SENSOR
- BREAKDOWN BOX
Buy product